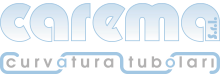
- Data
- Mar 18, 2025
- Anodizzazione, News
In questo articolo noi di Carema vogliamo parlarti, tra le varie tecniche di lavorazione che svolgiamo, di anodizzazione.
Anodizzazione: ecco di cosa si tratta
Quando si parla di anodizzazione, si fa riferimento ad un processo utilizzato per aumentare lo spessore degli strati di ossido naturale presente sulla superficie delle parti metalliche, anche se va detto che di solito è applicata a substrati in lega di alluminio, e dunque può essere applicata anche a titanio, zinco, magnesio, niobio, zirconio, afnio e tantalio.
Detto questo devi sapere che il processo di anodizzazione utilizza la passivazione elettrolitica per ottenere le proprietà desiderate, quali:
- La resistenza alla corrosione e all’usura;
- Una migliore adesione per vernici e colle;
- Effetti estetici.
Ma se ti stai chiedendo perché questo processo è chiamato esattamente così, devi sapere che è legato al fatto che il substrato di alluminio costituisce l’elettrodo anodico di un circuito elettrico. L’anodizzazione viene adottata anche per prevenire l’attrito o l’usura dei componenti filettati e per realizzare pellicole dielettriche per condensatori elettrolitici. La struttura microscopica di un pezzo e la struttura cristallina del metallo vicino alla superficie cambiano con l’anodizzazione. I rivestimenti spessi di solito richiedono un processo di sigillatura per prevenire la corrosione a causa della loro natura porosa. I film anodici sono vantaggiosi in quanto presentano una maggiore resistenza e proprietà adesive rispetto alla maggior parte dei tipi di placcatura metallica; tuttavia, sono anche più fragili, il che li rende più soggetti a cricche dovute a stress termico.
Per quanto riguarda invece i vantaggi dell’anodizzazione, devi sapere che sono l’ottenimento di uno strato significativamente più sottile rispetto alla vernice o alla polvere, estremamente durevole, duro, resistente all’abrasione e di lunga durata, nessuna sbucciatura o scheggiatura, superficie molto più dura della vernice, resistenza allo sbiadimento del colore, eccellente protezione dalla corrosione, rispettoso dell’ambiente, buon isolante elettrico e conveniente.
Se andiamo indietro nel tempo, ci accorgeremo che l’anodizzazione è stata introdotta per la prima volta in un contesto industriale nel 1923 per proteggere dalla corrosione le parti in duralluminio utilizzate negli idrovolanti. Inizialmente fu adottato l’uso dell’acido cromico, chiamato processo Bengough-Stuart. Alla fine, questo processo portò all’adozione dell’acido solforico, che divenne presto e rimane tuttora l’elettrolita anodico più comune. Nel 1923, l’anodizzazione con acido ossalico fu brevettata in Giappone e successivamente ampiamente adottata in Germania, soprattutto nelle applicazioni architettoniche. Negli Anni ’60 e ’70, l’estrusione di alluminio anodizzato rappresentava un materiale architettonico molto diffuso, ma è stato sostituito da materiali plastici più economici e dalla verniciatura a polvere. Più recentemente, l’acido fosforico è stato applicato al campo dell’anodizzazione, per ora utilizzato esclusivamente come pretrattamento per adesivi e vernici organiche.